Deep Integration of 5G Industrial Internet of ThingsXinhanze
Weifang New Hanze Energy Technology has a company's independent research and development of intelligent production line using 5G MEC (multi-access edge computing) architecture, to achieve the device layer, control layer, management of the three-level data exchange. Through the deployment of 2000 + sensor nodes, 300 + key parameters such as vibration, temperature and energy consumption of equipment such as silo, conveyor and mixing kettle are collected in real time. The data transmission delay is as low as 5ms, which is 90% higher than that of traditional wired scheme. For example, in the graphite purification link, 5G private network supports high transmission rate to monitor the temperature control facts of the reaction tank, and cooperates with AI algorithm to realize automatic adjustment of the reaction temperature, thus increasing the yield by 12%.
Full process automation control systemXinhanze
Based on the self-developed MES (Manufacturing Execution System), the production line realizes the whole process from raw material feeding to finished product packaging. Typical application scenarios include:
1. Intelligent batching: through the linkage of the Internet of Things weighing system and ERP system, the raw material ratio accuracy reaches +/-0.1, and manual intervention is reduced by 90%.
2. Reactive intelligent temperature control: 5G wireless temperature sensor is deployed, and heating curve is dynamically adjusted in combination with PID algorithm, energy consumption is reduced by 18%, and product consistency is improved by 25%.
3. Intelligent storage: AGV car is equipped with 5G positioning module to realize automatic material handling and improve logistics efficiency by 40%.
Digital Twins and Predictive Maintenance
Build a production line digital twin model to map the running status of physical equipment in real time. For example, through the spectral analysis of the vibration data of the roller press bearing, the accuracy of predicting equipment failure is 92%, and the maintenance cost is reduced by 35%. The technology has been applied to the Bertrand Group's 80000-ton anode material project in Indonesia, reducing equipment downtime by 60%.
1. Intelligent batching: through the linkage of the Internet of Things weighing system and ERP system, the raw material ratio accuracy reaches +/-0.1, and manual intervention is reduced by 90%.
2. Reactive intelligent temperature control: 5G wireless temperature sensor is deployed, and heating curve is dynamically adjusted in combination with PID algorithm, energy consumption is reduced by 18%, and product consistency is improved by 25%.
3. Intelligent storage: AGV car is equipped with 5G positioning module to realize automatic material handling and improve logistics efficiency by 40%.
Digital Twins and Predictive Maintenance
Build a production line digital twin model to map the running status of physical equipment in real time. For example, through the spectral analysis of the vibration data of the roller press bearing, the accuracy of predicting equipment failure is 92%, and the maintenance cost is reduced by 35%. The technology has been applied to the Bertrand Group's 80000-ton anode material project in Indonesia, reducing equipment downtime by 60%.
Production efficiency jumpsXinhanze
1. Single-machine capacity increase: Using 5G + AI vision inspection system, the detection rate of surface defects of negative electrode materials increased from 85% to 99.5, and the daily production capacity of a single production line increased from 120 tons to 180 tons.
2. Comprehensive efficiency optimization: Through the intelligent scheduling system, the OEE (comprehensive efficiency) of the equipment is increased from 65% to 82%, and the annual production capacity is increased by 30%.
2. Comprehensive efficiency optimization: Through the intelligent scheduling system, the OEE (comprehensive efficiency) of the equipment is increased from 65% to 82%, and the annual production capacity is increased by 30%.
Significant cost optimizationXinhanze
1. Labor cost: the whole process automation reduces the number of operators in a single production line from 35 to 8, and the labor cost is reduced by 77%.
2. Energy consumption cost: through real-time monitoring of the energy management system, the power consumption per unit product is reduced from 850kWh to 680kWh, saving 2.6 million yuan per year.
3. Cost of quality: The rate of defective products decreased from 3.2 per cent to 0.8 per cent, reducing the annual loss of quality by more than 5 million yuan.
2. Energy consumption cost: through real-time monitoring of the energy management system, the power consumption per unit product is reduced from 850kWh to 680kWh, saving 2.6 million yuan per year.
3. Cost of quality: The rate of defective products decreased from 3.2 per cent to 0.8 per cent, reducing the annual loss of quality by more than 5 million yuan.
Safety and environmental upgradeXinhanze
1. Replacement of dangerous links: In graphite powder transportation, high-temperature kiln operation and other scenes, the robot replacement rate reached 100 percent, and zero work-related accidents occurred.
2. Environmental compliance: 5G water quality monitoring system will be deployed, the wastewater treatment efficiency will be increased by 40%, and the COD emission concentration will be lower than the national standard by 50%.
2. Environmental compliance: 5G water quality monitoring system will be deployed, the wastewater treatment efficiency will be increased by 40%, and the COD emission concentration will be lower than the national standard by 50%.
Selected field cases
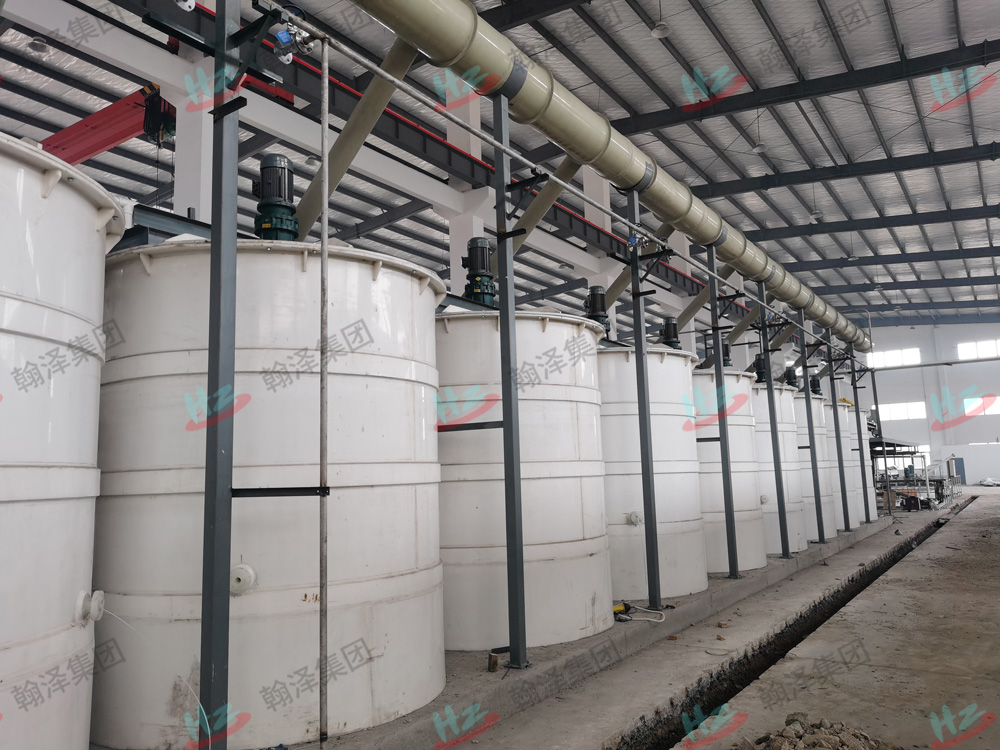
Carbon nanotube purification production line
Fujian, China
Anode Materials for Sodium Batteries
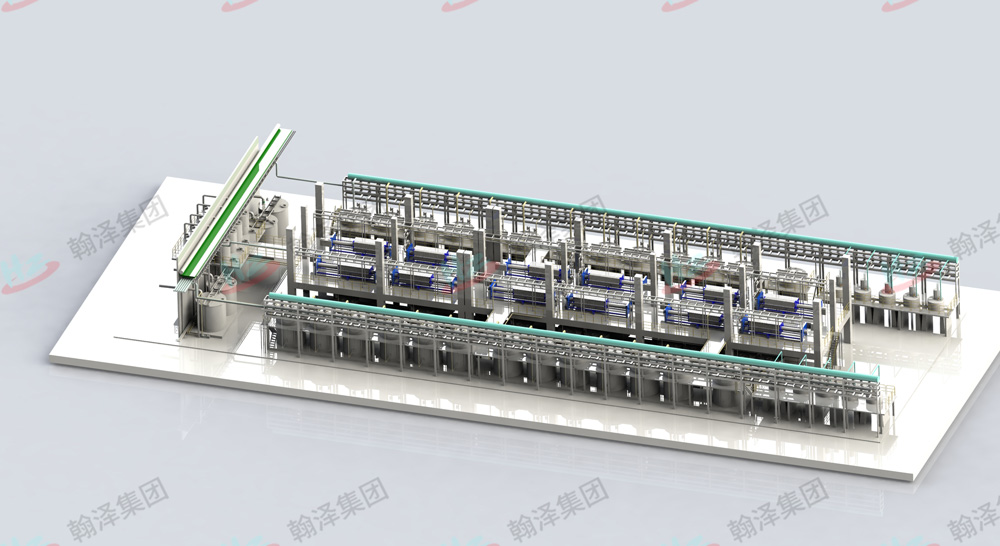
Overseas project site
Indonesia
Unknown
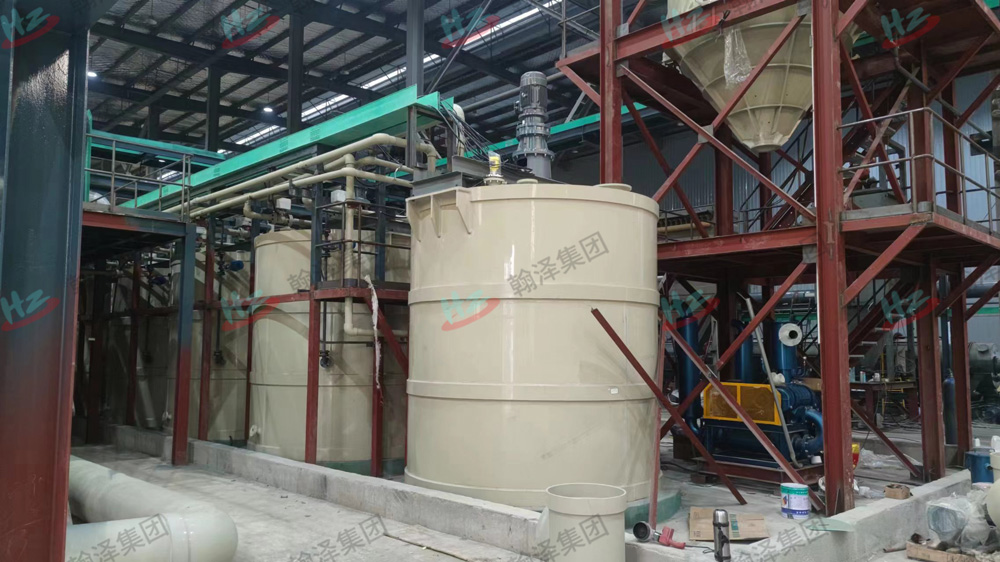
Recycled negative material purification production line
Anhui, China
Recycled negative material
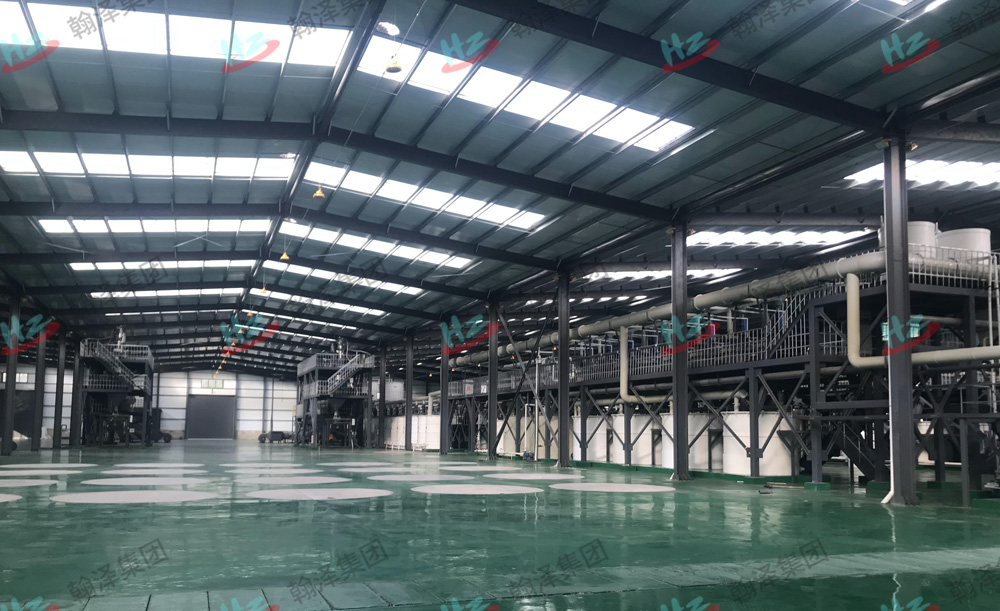
Expandable graphite production line
China
expandable graphite
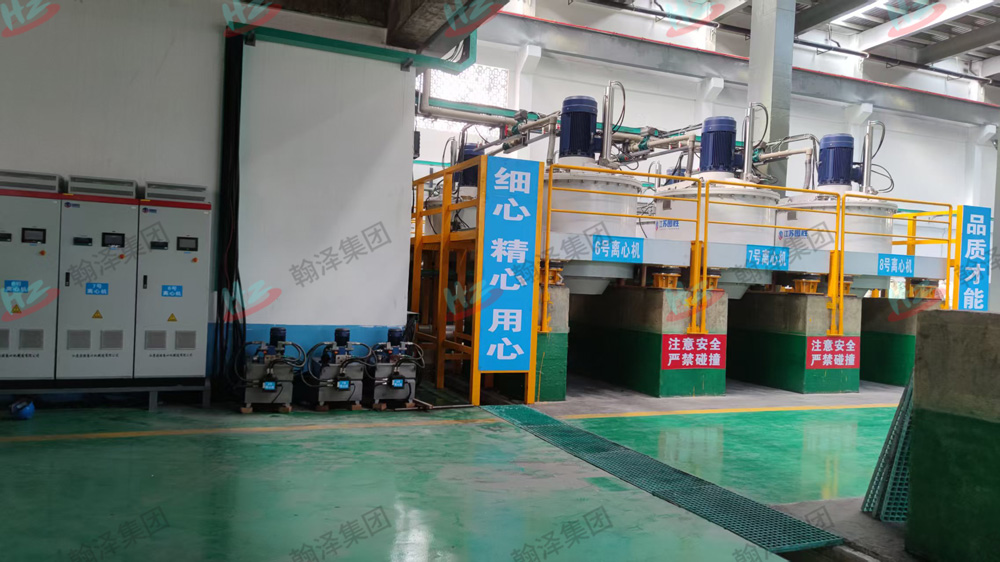
Natural purification production line
China
natural graphite
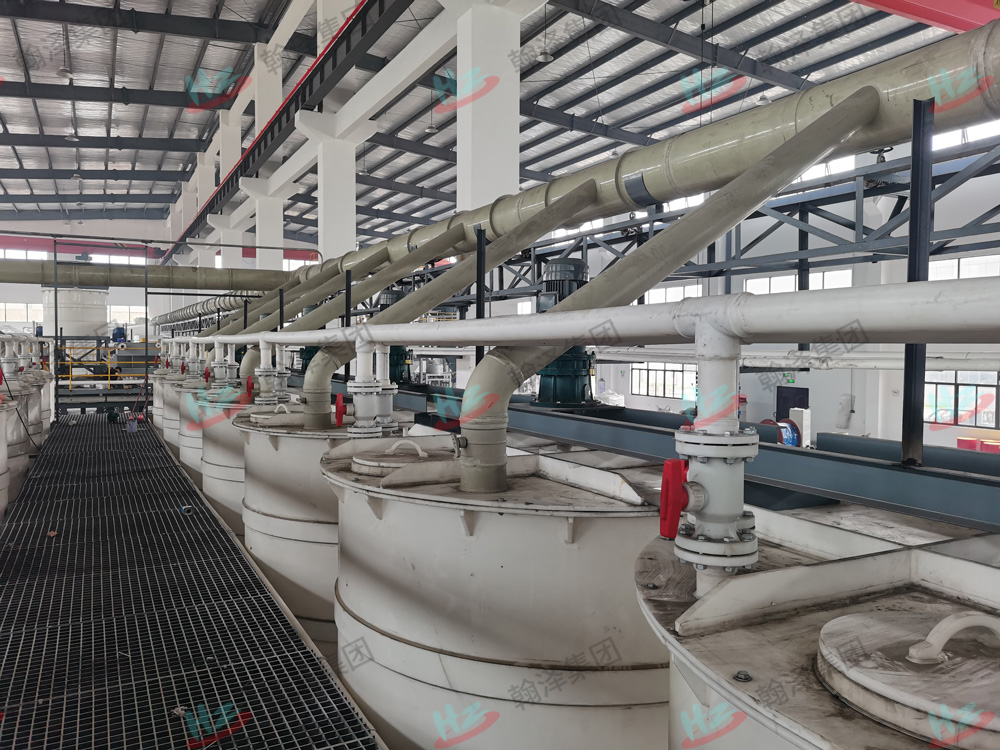
Sodium-Hard Carbon Purification Line
Fujian, China
nano battery
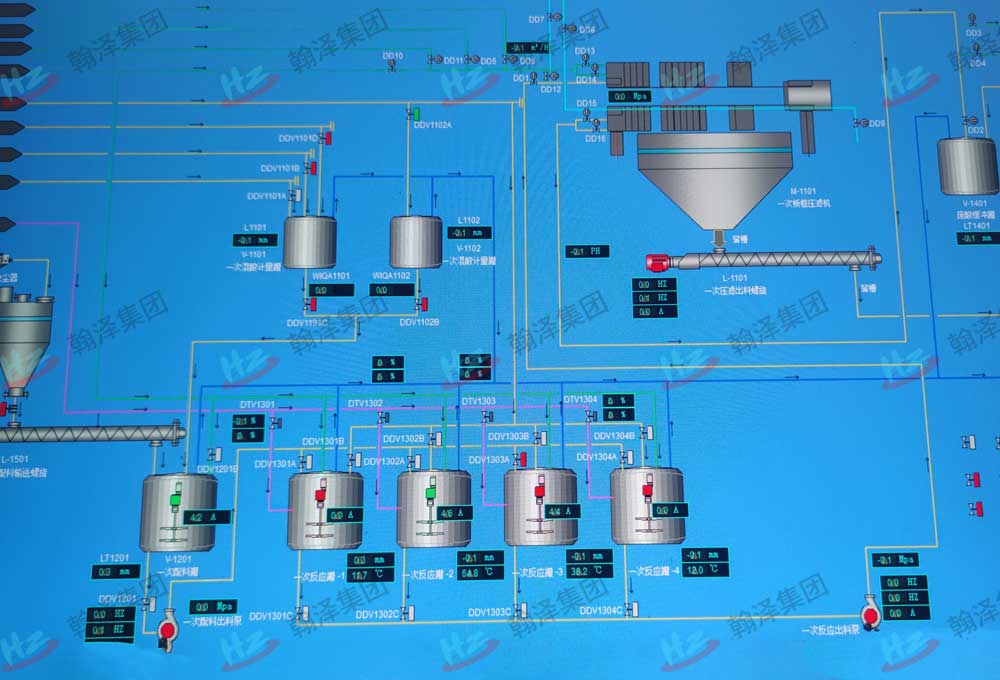
automatic control system
China
Unknown
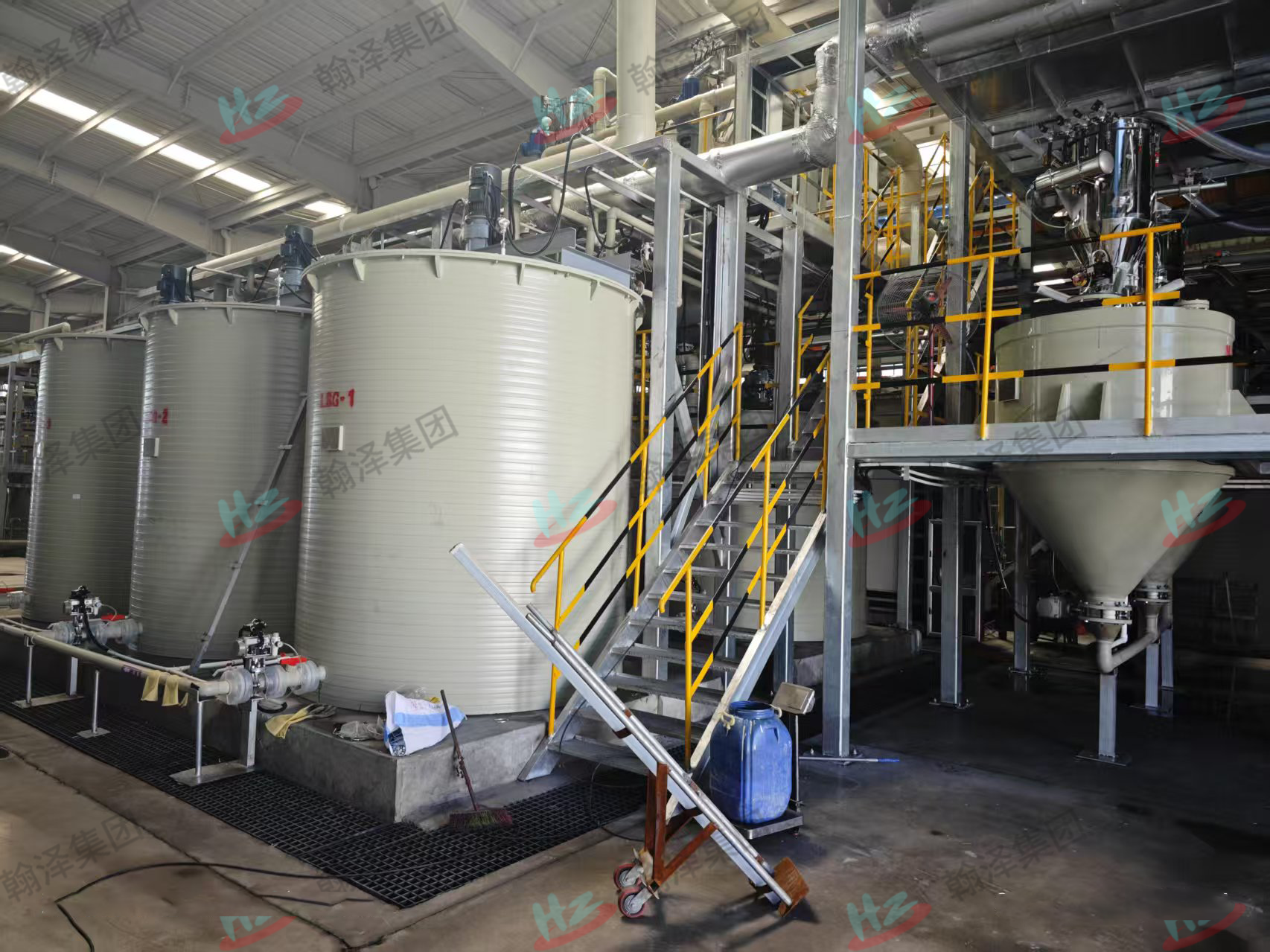
porous carbonic acid washing production line
China
porous carbonic acid washing
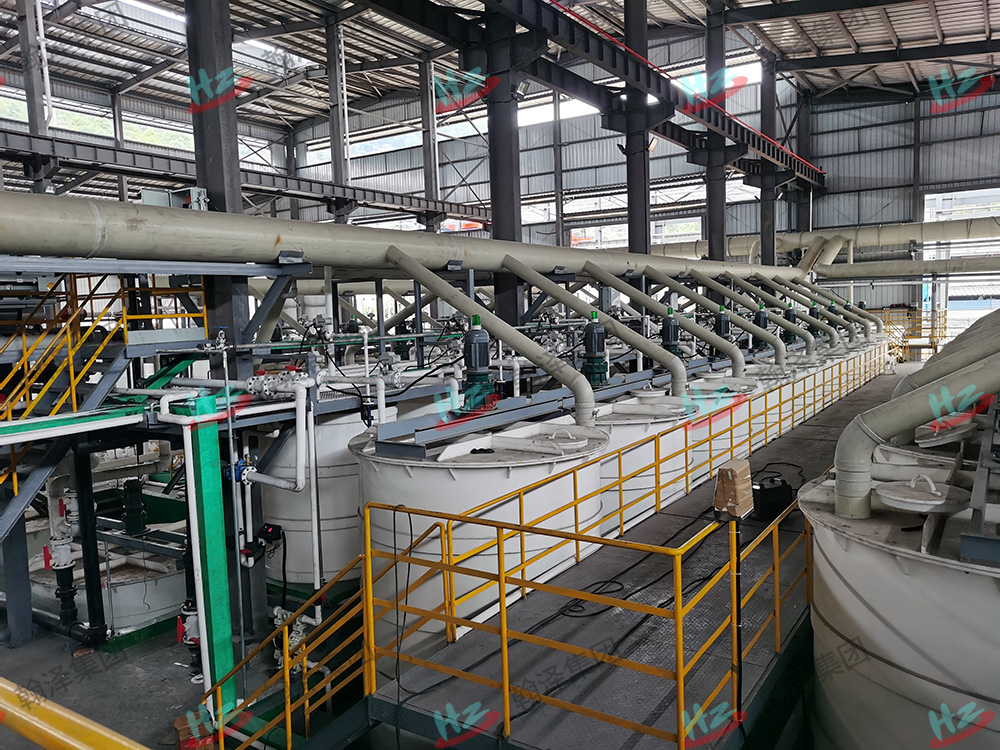
Quartz sand pickling production line
China
Quartz sand pickling
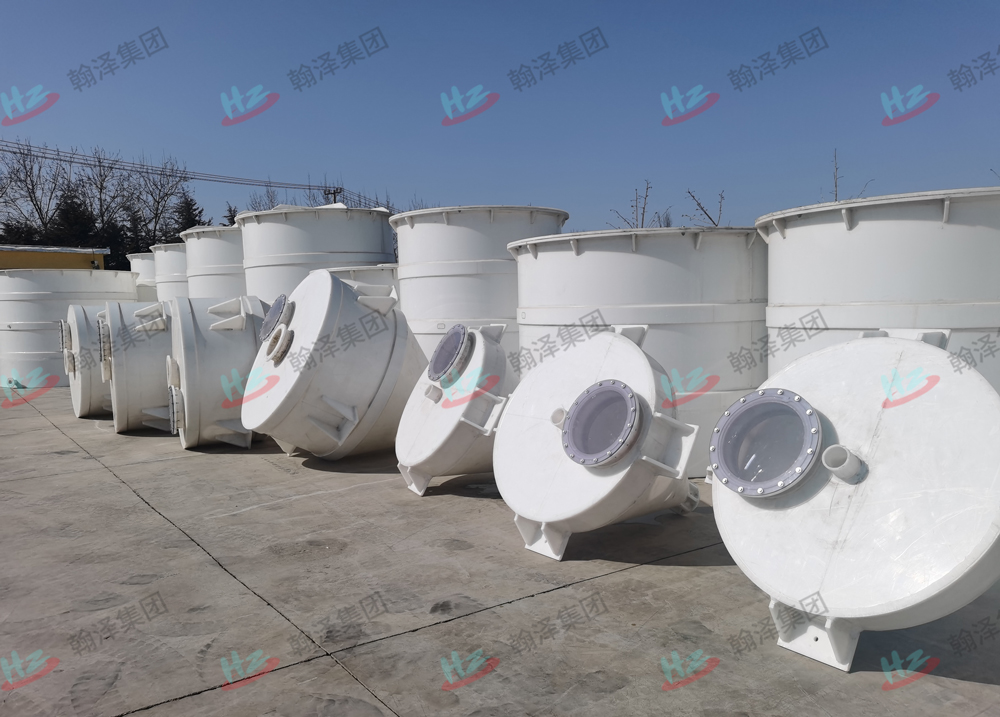
PPH Equipment
China
PP Equipment